Adding intelligence to the industrial maintenance with a novel decision support system.
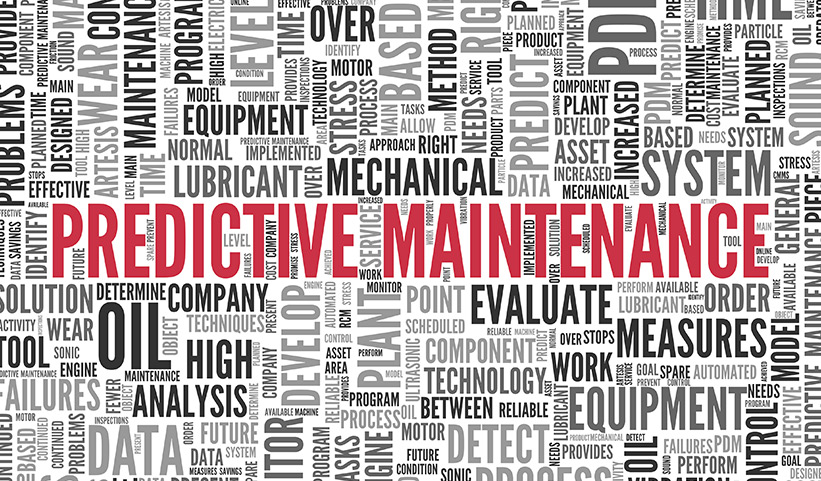
Project iMAIN: A novel decision support system for intelligent maintenance.
“iMAIN” is a European level research project aiming to develop a novel decision support system for predictive maintenance. To that end, a multi-layer solution integrating embedded information devices and artificial intelligence techniques for knowledge extraction and novel reliability & maintainability practices is developed. The resulting solution provides extended capabilities compared to those achievable with current state-of-the-art maintenance practices, increasing system lifetime of the production equipment, energy efficiency, maintenance cost and availability of whole process at least.
As for maximizing project impact, “iMAIN” project is strongly committed to deployment issues, including innovation and implementation actions focused on value chains and bridging the gap from research to market. To that end, “iMAIN” emphasizes on the commercialization of results, taking also into account the needs of post-project monitoring of commercialization, which will be conducted after the end of the project in order to assess the achievement of the requested funding and for promoting the project as an effective innovation mechanism.
As a step towards the Europe 2020 strategy, “iMAIN” project is thus contributing in terms of R&D investment, employment and resource efficiency, aiming to assist EU manufacturers, particularly SMEs, to adapt to global competitive pressures by increasing the technological base of EU manufacturing through the development and integration of the enabling technologies of the future, specifically engineering technologies for novel predictive maintenance solutions.
Our main tasks
- Development and simplification of complex stress finite element method (FEM) simulation models for the detection of failure-critical zones (so called cMODEL) of press equipment.
- Development and implementation of the IT infrastructure concept of the simulation environment, considering simulation needs, the necessary interfaces to the cloud and to the Embedded Condition & Energy Monitoring (so called ECEM) system, and data processing capabilities.
- Development of the so-called eMODEL, a model aimed to provide predictive energy consumption analysis in production environments, so as to allow the virtual testing of different future load scenarios (e.g. derived by offline process simulation or from former real loads, stored from data history) via user interface.
- Development of the smart service life prediction system, which is aimed to predict the remaining service life as a function of load history, actual and future loads and conditions.
- System integration, testing and validation strategy in a hydraulic and a mechanical forming press.
- Knowledge dissemination to the international R&D community.
Partners
ADVANTICSYS | FRAUNHOFER IWU | GORENJE | IDENER.AI | IMC | LITOSTROJ RAVNE | RUBICO CONSULTING | UNIVERSITY OF LULEA
Start date – finish date
09 / 2012 - 08 / 2015
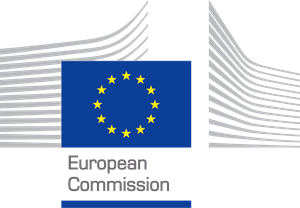
This project has received funding from the European Union